Light Detection and Ranging (LiDAR) uses laser light to measure the distance to surrounding objects and features. LiDAR is fast becoming a leading technology in 3D sensors for autonomous vehicles and industrial robots.
LiDAR provides very high resolution dimensional imagery at high speeds—which means accuracy in manufacturing is crucial. Kasalis systems precisely align and assemble optical components, aligning the projector to the receiver within the device using scope tracing algorithms, thereby creating the most accurate solutions on the market.
Industry Challenges
Active alignment in 6DOF with 50 nm accuracy
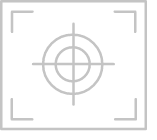
Integrated process monitoring systems and product tracking
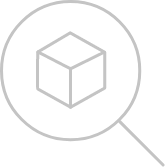
Athermalized product design capability and materials selection
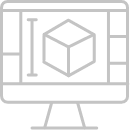
Customized interface electronics integrated into active alignment fixtures
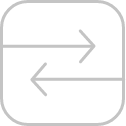
Multi-dispense-align-cure steps

Customized optical feedback systems and algorithms for unique product architectures
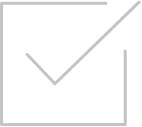
Projector aligned to receiver using scope-tracing algorithms
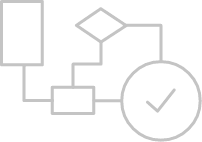
Active alignment in 6DOF with 50 nm accuracy
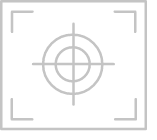
Integrated process monitoring systems and product tracking
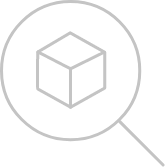
Athermalized product design capability and materials selection
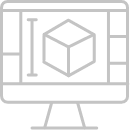
Customized interface electronics integrated into active alignment fixtures
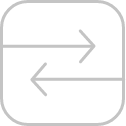
Multi-dispense-align-cure steps

Customized optical feedback systems and algorithms for unique product architectures
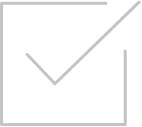
Projector aligned to receiver using scope-tracing algorithms
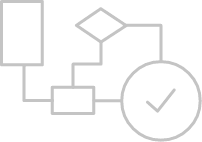
Product Information
Our Pixid systems can assemble and align solid state or mechanical LiDAR optical devices that are the most precise in the industry—and that can be customized to specific manufacturing needs.
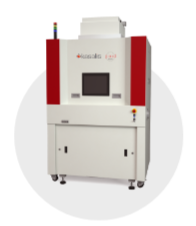
PIXID 500-S
Enhanced capability, automated active alignment system with assembly and test capabilities with single head
DOWNLOAD DATASHEET |
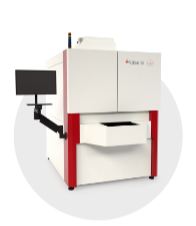
PIXID 700
Highest accuracy system with nano-precision option and specialized mechanics
DOWNLOAD DATASHEET |